فرآیند تولید لوله و پروفیل فولادی
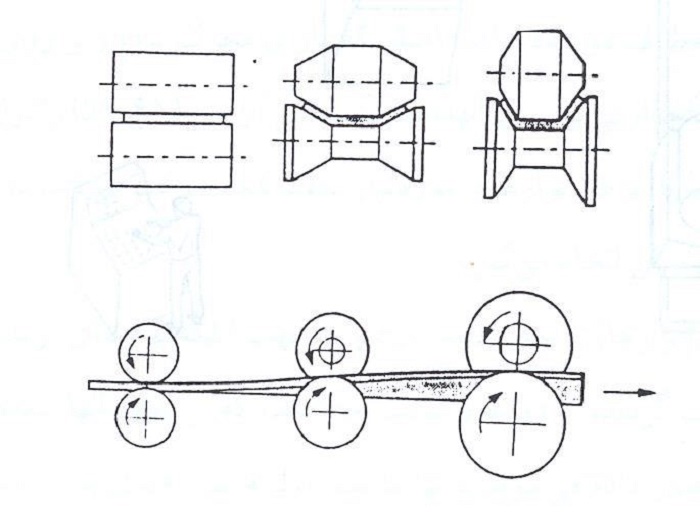
كار عمده كارخانجات لوله و پروفیل تبدیل ورق فولادی(كلاف) به روش نورد سرد به محصول نهایی با شكل ها و ابعاد مختلف (پروفیلهای باز و بسته) می باشد. این فرآیند شامل مراحلی می باشد که ذیلاً به اختصار توضیح داده می شود :
1 _ مواد اولیه :
مواد اولیه مصرفی اكثر كارخانجات قبل از راه اندازی فولاد مباركه از كشورهای اروپایی و ژاپن تأمین می گردید ولی در حال حاضر قسمت عمده آن ازطریق فولاد مباركه و قسمتی نیز از كشورهای آسیای میانه، برزیل، اروپا و اروپای شرقی تهیه می گردد.
ورق مصرفی باید دارای تركیبات شیمیایی خاص بوده و بالطبع از خواص مكانیكی مناسبی برخوردار باشد تا در هنگام تولید برای سازنده و در نهایت برای مصرف كننده ایجاد مشكل ننماید. ورق مصرفی با استاندارد 37.2 ST و یا JIS G 3131 یا G 3132 دارای تركیبات شیمیایی (سیلیس با 35/0 ، كربن با 3/0 تا 1/0 ، گوگرد 04/0 ، فسفر 04/0 ، منگنز 5/0) بوده و برای اینگونه تولیدات پیشنهاد و مورد مصرف می باشد مگر در موارد خاص.
ورق فولادی پس از ورود به كارخانه توزین و باتوجه به مشخصات ابعادی و مصرف آنها در قسمت های مختلف، انبارشده تا وارد پروسه تولید گردد.
2 _ برش كلاف به نوار :
كلاف های خریداری شده در دستگاه های برش به نوارهایی با عرض مشخص بریده می گردند. این دستگاه ها بنا به سفارش و نحوه بهره برداری دارای قسمت های مختلف بوده كه بعضاً تمام اتوماتیك و برخی نیمه اتوماتیك می باشند.
یک دستگاه برش معمولا دارای قسمت های ذخیره کلاف، میز حمل کننده، ضربه گیر، کلاف گیر، و سیستم بازکننده طوقه های کلاف، سیستم كنترل كننده كناره كلاف برای بهتر تنظیم شدن، صاف كننده ورق، گیوتین و قرقره های هدایت ورق، غلتك های تغذیه ورق، قسمت اصلی برش، غلتك های جداكننده نوارهای بریده شده، نگاه دارنده نوارها و نهایتاً نوار جمع كن می باشد.
پس از قرار گرفتن كلاف روی كلاف گیر كه خود نیز دارای حركت گردشی می باشد كلاف گیر چرخیده و پس از بازشدن طوق ها سر ورق زیر غلتك های صاف كننده هدایت می گردند. این عمل باعث صاف و تخت شدن ورق می گردد. توسط گیوتین سر ورق بریده شده تا برای جوشكاری در قسمت های بعدی اشكالی وجود نداشته باشد. آنگاه ورق توسط غلتك های تغذیه به طرف دو عدد شافت اصلی كه دارای محرك بوده و بر روی آن تیغه هایی از فولاد كه عملیات حرارتی بر روی آنها انجام و سختی آن بین (61-59) راكول سی رسیده و فواصل آنها متناسب با عرض نوارهای موردنیاز تنظیم شده حركت می كند. دراثر عبور ورق از بین دو تیغه عمل برش انجام می گیرد.
حركت ورق(نوارها) به جلو ادامه دارد و به جهت اینكه نوارهای بریده شده به طور دقیق به جلو هدایت گردند، از دو عدد شافت جداكننده كه بر روی آنها تیغه های كوچكی مستقر گردیده اند عبور داده می شوند تا نهایتاً سر اولیه نوارهای بریده شده در گیره مخصوصی كه در داخل نوار جمع كن قرار دارد و توسط سیستم هیدرولیك قطر نوار جمع كن را چند سانتیمتر باز می نماید درگیر شود. این عمل از یك طرف باعث جمع شدن دولبه گیره و گرفتن سر نوارها شده و ازطرفی در پایان زمان تخلیه نوارها با عمل جمع شدن نوارگیر از داخلی ترین لایه ورق ها جداشده و به سهولت می توان نوارها را توسط میز متحرك و صفحه ای كه در جهت محور اصلی حركت می كند به خارج هدایت نمود. از این مرحله به بعد عمل كشیدن ورق توسط نوار جمع كن تا تمام شدن كل طول كلاف انجام می گیرد. نوارها نهایتاً دسته بندی و به قسمت های مختلف خطوط تولید انتقال می یابد.(شكل 1-4)
شكل (1-4) : نمایی از خط نوار بری
3 _ تولید لوله و پروفیل :
قوطی و پروفیل را می توان به دوطریق مستقیم و غیرمستقیم تولید نمود. روش انتخابی بستگی به امكانات ماشین ازنظر طراحی دارد. معمولا پروفیل به روش مستقیم تولید می گردد. دستگاه های لوله و پروفیل عموماً دارای قسمت های تغذیه نوار، گیوتین، قسمت جوش سر و ته نوار، انباره، فرمینگ(كه از دوقسمت شكل دهنده اولیه و شكل دهنده نهایی ، قسمت جوش دولبه پروفیل، براده برداری، سردكن، سایزینگ با تعداد 4 تا 6 دروازه خمش و پیچش گیر برش(اره) اتوماتیك ، شتاب دهنده و نهایتاً میز تخلیه می باشند. باتوجه به اینكه دستگاه برای ساخت چه تولیداتی طراحی شده و به چه روشی ساخته شده باشد قسمت های فوق باكمی تغییر از نظر تعداد و اندازه ساخته خواهد شد ولی آنچه قابل ذكر است اینكه عمل اصلی این دستگاه ها شكل دادن به ورق در حال عبور از بین دوقالب بالا و پایین درحال چرخش در دروازه های مختلف تا تولید محصول نهایی به طریقه سرد می باشد. (شكل 2-4)حالتی از شكل گرفتن نوار فلزی را نشان می دهد.
شكل (2-4) : نحوه تولید یك نوع پروفیل
تولید پروفیل و قوطی های ساختمانی می تواند به روش مستقیم و یا غیرمستقیم (تولید لوله و سپس تبدیل به شكل نهایی) انجام گردد. هر روش دارای محاسن و معایبی می باشد.
در روش تولید مستقیم نوار در اثر عبور ازبین قالب های بالا و پایین (دارای محرك) و دركنار هرزگردها كه طراح با انجام محاسبات ازنظر میزان نیرو و زوایای شكل موردنظر كه با توزیع در هر دروازه طراحی نموده به تدریج شكل گرفته و پس از جوش خوردن دولبه ورق توسط جوش های فركانسی نهایتاً در قسمت سایزینگ شكل كامل می گیرد.
كاملا جوش قالب ها و حرارت نیرو ازطرف در اثر اعمال تولید شده پروفیل مستقیم نبوده و توسط پیچش گیر با اعمال نیروی مجدد، خمش، پیچش و كمانش آن اصلاح می گردد. پروفیل درحال تولید، توسط اره اتوماتیك در فواصل 6 متری بریده و به تعداد معینی بسته بندی و پس از نصب كارت مشخصات و تأیید كنترل كیفی به انبار محصولات تحویل می گردد.
در روش تولید غیرمستقیم پروفیل ابتدا در دستگاه اصلی نورد با همان مراحل فوق و یكی از سه روش خم كردن، به لوله تبدیل و پس از جوش دولبه، در قسمت سایزینگ و پیچش گیر دراثر فشارهای بالائی و پایینی و جانبی، این لوله به اشكال مختلف تبدیل می گردد و یا اینكه در قسمت سایزینگ و پیچش گیر لوله كامل تر و محصول نهایی لوله خواهد بود و پس از برش بسته بندی می گردد.
لوله های تولید شده را در دستگاه های ساده تری كه هر یك دارای 8 الی 10 دروازه می باشند عبور داده و اشكال مختلفی را تولید خواهند نمود.
محاسن و معایب دو روش :
الف روش مستقیم :
پروفیل تولید شده به روش مستقیم دارای زاویه های تیز، ابعاد دقیق و خط جوش ثابت در دیواره بالایی و انحنای سطحی كم بوده و نسبت به روش دیگر از كیفیت بالاتری برخوردار خواهد بود.
در این روش به دلیل تیز گوشه بودن و اختلاف قطر نقاط مختلف قالب ها و سرعت خطی متفاوت، استهلاك قالب ها بیشتر می باشد. همچنین ازنظر ماشین كاری و عملیات حرارتی نیز دقت عمل بیشتری لازم است از طرفی فضای هوایی بیشتر بین ایندكتور و پروفیل و فریت سرعت تولید را كاهش داده و نسبت به روش تولید غیرمستقیم دارای سرعت كمتر و راندمان پایین تری خواهد بود(شكل 3-4)
شكل (3-4) : تولید پروفیل به روش مستقیم
ب روش غیر مستقیم :
در این روش در قسمت اولیه ماشین (شامل forming و finishing) به یكی از سه طریق : شكل دهی لبهای، شكل دهی مركزی و یا شكل دهی ازطریق شعاع واقعی (شكل 4-4)
(باتوجه به نظر طراح و شرایط ماشین) نوار به لوله تبدیل و در قسمت sizing به شكل موردنظر تبدیل می گردد كه این روشon line نامیده میدشود و یا پس از اینكه در این دو قسمت نیز لوله كامل و بریده شد، در دستگاه های دیگری عمل تغییر شكل انجام می گردد. در این روش چون می توان با ساخت یك لوله در قسمت فرمینگ و تعویض حداقل چند قالب در قسمت سایزینگ و یا بردن به دستگاه های بدون جوش دیگر چند نوع پروفیل تهیه نمود داشتن تنوع پروفیل با حداقل ماشین لوله سازی امكان پذیر است .ضمناً چون فاصله هوایی بین ایندكتور و لوله به حداقل ممكن و قطر انتخابی فریت می تواند به بالا ترین اندازه ممكن برسد از حداكثر توان دستگاه جوش میتوان استفاده كرده و سرعت تولید نسبت به روش مستقیم بیشتر خواهد بود. قالب ها منحنی شكل و ساخت با دستگاه راحت تر و در عملیات حرارتی احتمال شكستن به دلیل عدم وجود گوشه های تیز بسیار كمتر می باشد ولی ازنظر كیفیت، گوشه ها گردتر و اندازه اضلاع و خط جوش و انحنای سطحی بادقت پایین تر نسبت به روش مستقیم خواهد بود.
چنانچه تولید لوله صرفاً برای تهیه لوله گاز و یا آب باشد قطر لوله را در قسمت جوش حدود نیم میلی متر بیشتر از قطر نهایی ساخته و این میزان اضافه قطر لوله را با افزایش سرعت خطی به وجود آمده در اثر افزایش قطر قالب ها در هر دروازه (5/0 تا 2/0) میلیمتر در سایزینگ تقلیل داده و عملا لوله را كشیده و گرد می نمایند. لوله تولید شده را می توان قبل از برش توسط تست غیر مخرب ادی كارنت (حوزه مغناطیسی) آزمایش و یا پس از برش به صورت off line آزمایش را انجام داد و آنگاه پس از پلیسه گیری عمل تست هیدرواستاتیك را تا فشار حدود 70 بار برای مدت 5 ثانیه انجام داده پس از تأیید و چاپ مشخصات لازمه بر روی لوله ها به صورت شش گوش بسته بندی و به بازار عرضه نمود.
شكل (4-4) : سه روش شكل دهی متداول لوله
محاسبه عرض نوار:
عرض نوار مصرفی موردنیاز برای یك مقطع با استفاده از رسم طرح مقطع با مقیاس بزرگتر معین می گردد. بدین صورت كه اندازه قسمت های صاف و اندازه قسمت های خمشده كه در اثر تنش یا كشش درطول محور خنثی به دست آمده را جمع می كنند. عدد به دست آمده به نسبت مقیاس، تعیین كننده عرض نوار مصرفی خواهد بود. برای شعاع های داخلی كه معادل 2 برابر ضخامت مواد اولیه باشد محل محور خنثی را تقریباً در13 فاصله بین سطح خارجی و داخلی خم درنظر می گیرند چنانچه عرضی كه در اثر تنش یا كشش به وجود آمده است را باω كه با نام خم مجاز شناخته میشود نمایش دهیم برای قسمت خم شده با شعاع داخلی معادل t2 از رابطه زیر به دست می آید:
ω = 0.01745 α (r + t/3) عرض گوشه
در رابطه بالا α زاویه خم برحسب درجه و r شعاع داخلی خم به میلی متر و t ضخامت فلز مصرفی می باشد و عدد 0.01745 عامل تبدیل درجه به رادیان درنظر گرفته شده است.
هرگاه خم موردنظر تیز باشد شعاع داخلی تقریباً به صفر نزدیك و r از رابطه بالا حذف می گردد درنتیجه داریم:
ω = 0.01745 α (t/3)
زمانی كه شعاع داخلی خم برابر یا بیشتر از t 2 باشد و یا اینكه مواد اولیه از شكل پذیری كمتری نسبت به فولاد با كربن پایین برخوردار باشد و یا هردو عامل فوق الذكر موجود باشد محور خنثی تقریبا بین سطح داخلی و خارجی خم قرار می گیرد و در رابطه فوقt/3 به t/2 برای محاسبه عرض نوار تغییر می كند:
ω = 0.01745 α (r + t/2)
همانگونه كه قبلاً اشاره شد سه روش برای خم كردن مشخص شده كه هر یك با تعداد دروازه های متفاوت بوده و این بستگی به ضخامت ورق مورد مصرف و تركیب شیمیایی فولاد دارد.
هرچه ضخامت ورق مصرفی بالاتر و نوع تركیبات ورق فولادی مصرفی سختی بیشتر داشته باشد به تعداد دروازه بیشتری نیاز می باشد و چنانچه تعداد دروازه ها كم باشد نهایتا موجب ناصافی و پیچ خوردگی شاخه می گردد.
مختصری درمورد جوش لبه ها:
عمل جوش دو لبه لوله و یا پروفیل به وسیله جوش های فركانسی انجام می گیرد. بدین صورت كه چون تلفات درتمامی سیستم ها با مجذور فركانس رابطه مستقیم دارد، ابتدا ولتاژ (380) ولت سینوسی شبكه توسط ترانس افزاینده به میزان 10 كیلوولت افزایش پیدا كرده سپس این ولتاژ توسط 6 سری ركتی فایر به صورت یك ولتاژ DC درآمده ولتاژ حاصله پس از صاف شدن و كاهش نوسان، فاكتور آن به یك لامپ تریود با توان بالا اعمال كه در این مرحله لامپ با ایجاد نوسان ، ولتاژ DC را به صورت یك ولتاژ سینوسی با فركانس موردنیاز (حدود 400350 كیلوهرتز) مناسب برای جوش پروفیل تبدیل می نماید)فركانس موردنیاز توسط سلف و تعدادی خازن تعیین می گردد.( این ولتاژ توسط ترانس مجدداً كاهش پیدا كرده و به ایندكتور منتقل می گردد.
ایندكتور، مشابه سیم پیچ اولیه یك ترانس، و لوله به صورت ثانویه و ذغال به عنوان جمع كننده یا هسته مورداستفاده قرار می گیرد. درحال حاضر با پیشرفت تكنولوژی به جای استفاده از لامپ تریود از قطعات الكترونیكی بنام mos استفاده میكنند كه تعدادی mos با كانال N در مسیر خط + و تعدادی mos با كانال P در مسیر خط قرار گرفته و فركانس موردنظر را به وجود می آورند كه مزیت اینگونه سیستم ها در تغییر قدرت خروجی با استفاده از تعویض كارت های mos و همچنین عدم استفاده از ولتاژ 10 كیلوولت می باشند.
در شكل(5-4) شرایط ایندكتور ازنظر عرض، فاصله تا قالب های جوش، زاویه ورق درحال تبدیل به لوله وضعیت قرارگرفتن فریت (ذغال) نسبت به قالب های جوش مشخص شده است. تا بهترین راندمان را در قسمت جوش داشته باشیم:
αزاویه بسته شدن لوله نسبت به آخرین قالب2<α<3
عرض ایندكتور = 1L
فاصله شروع ایندكتور از مركز قالب جوش = 2L
1L را معمولاًبه اندازه قطر لوله درحال تولید درنظر می گیرند
معمولا فریت انتهای 3 تا 5 میلیمتر از مركز قالب های جوش باید جلوتر باشد
شكل (5-4) : شرایط قرارگرفتن ایندكتور